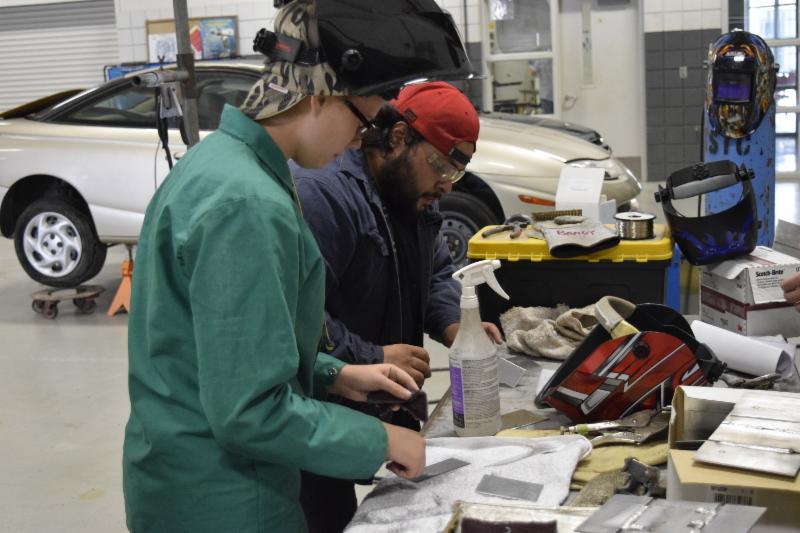
Texas State Technical College students (l to r) Kaitlyn Mackey and Roy Rodriguez work in the lab portion of the Advanced Collision Repair Welding course.
(WACO) – Kaitlyn Mackey, 17, said she has come a long way from being intimidated when she began welding several months ago. Now, she is confident she can find her focused zone to work.
“My favorite part is when I take off my helmet and look at the welding and it looks good,” said the dual enrollment Connally Early College High School senior and Texas State Technical College student.
Some students at TSTC are getting their first chance to work with automotive aluminum welding to make themselves more marketable in the workforce. The vehicle industry saw the unveiling this year of the Ford F-150, the first mainstream high-volume vehicle with an aluminum body.
“Steel vehicles have to be made lighter and stronger by thinning the metal, which is done by using advanced steels to maintain integrity,” said Ranson Bandy, an instructor in Auto Collision and Management Technology in Waco. “Using aluminum means vehicles can be made lighter with increased thickness and strength in the body.”
Bandy is teaching four students during fall semester in the Advanced Collision Repair Welding course. The class was developed because of the need for technicians to have knowledge and experience with new vehicle constructions due to the federal government’s mandate for higher miles per gallon. And, aluminum is almost 60 percent lighter than steel of the same thickness.
The learning material was developed from the Inter-Industry Conference on Auto Collision Repair, a not-for-profit organization advocating research, training and work in the collision field and from Original Equipment Manufacturer recommendations and service procedures. Students are learning about aluminum pulse spray arc welding, rivet bonding and silicon bronze welding which are all advanced forms of fastening these vehicles together.
“It’s pretty fun so far,” said Jordan Eppler, 21, of Valley Mills and second-year major in Auto Body Refinishing and Auto Collision Repair. “I do not know much about the aluminum body. I know it’s going to get complicated later on, but I like challenges.”
Roy Rodriguez, 23, of Clifton graduated from TSTC in 2014 with an associate degree in Automotive Technology and returned to learn about auto collision and painting. He wants to eventually work at a collision shop.
“I feel like today’s cars are getting so much better,” Rodriguez said. “So far the class is good. I have seen a big difference in welding with steel and aluminum. Whenever steel gets hot it glows, but aluminum doesn’t glow. That’s a tricky thing right there.”
Joe Keggler, 39, of Nacogdoches and Waco, is working on an associate degree in Auto Collision and Management Technology – Refinishing Specialization.
“A lot of the cars are becoming aluminum and I wanted to get the basics down before I go into the workforce,” Keggler said.
The class will culminate with an end-of-semester project. Students have three days to do a rail sectioning procedure which will include several forms of fastening techniques learned throughout the semester. Students must pay close attention to detail in the welding, quality and durability of the repair, Bandy said.
The class will also be offered in the spring, Bandy said.
Students can study Auto Collision and Management Technology at TSTC’s campuses in Waco and Harlingen.